
- #PARALLEL PORT CNC SOFTWARE DRIVERS#
- #PARALLEL PORT CNC SOFTWARE DRIVER#
- #PARALLEL PORT CNC SOFTWARE 32 BIT#
I believe this is due the cleaner pulse stream that lacks the beats between the base thread frequency and the requested step rate. This means that if we have realized a machine with a. We have had customers that have seen improvements in maximum step rate without stalling even if software steppingĬan generate the required step rate. Luckily all software used to drive a CNC machine implements functions to invert the polarity of every pin. The board has been tested with MACH3 CNC.
#PARALLEL PORT CNC SOFTWARE DRIVER#
All inputs and outputs except spindle can be used for other opeatations by software settings. Parallel port I/O break out board designed for Hobby CNC, Routers and Motion controller, This Board is an easy solution to driver stepper Motor driver, AC Servo (with Step-DIR Driver) and DC servo (with Step-DIR Driver), The Board is compatible with various CNC software specially made for LPT port data out. This may not bring any advantages if you are already limited by drive/motor speed limitations and don't use high resolution encoders. Parallel Port Buffered Breakout Board for 3 or 4 Axis CNC. So all of LinuxCNC's features are available regardless of the external hardware chosen, from Parallel port up to a fancy Ethercat motor drive.Īs Andy and Todd have said the main advantage of Mesa (or Pico or other) hardware is that they can generate faster and cleaner pulse streams and count encoder pulses faster as well. One of the nice design decisions in LinuxCNC is that all the complicated motion operations are done by the host CPU For our younger readers the parallel port is an interface standard used for bi-directional communication between a computer and a variety of peripherals. I have heard rumors that the port wont work under Windows 7. I have a port on my PC but have never used it. The problem is it uses a parallel port on the PC for the controller. Please Log in or Create an account to join the conversation. I am still thinking about taking the plunge and buying one of those cheap CNC printers. It can be run on a Windows 10 64bit operating system with specialized hardware adapters.
#PARALLEL PORT CNC SOFTWARE 32 BIT#
It only works on 32 bit PC’s up to Windows 7 with the parallel port driver, to control the motion of the stepper motors by processing G-Code.
#PARALLEL PORT CNC SOFTWARE DRIVERS#
But any performance gains would still be limited by the motors (impedance, voltage, etc) drivers I'm using, and the design limits of my router itself. The Mach3 software turns a Windows 32-bit computer into a CNC machine controller. It also seems that it would be possible to get more performance from the mesa cards because they can generate faster step pulses. My understanding is that the mesa card would give you a LOT of additional configuration options that you don't have with the parallel port.
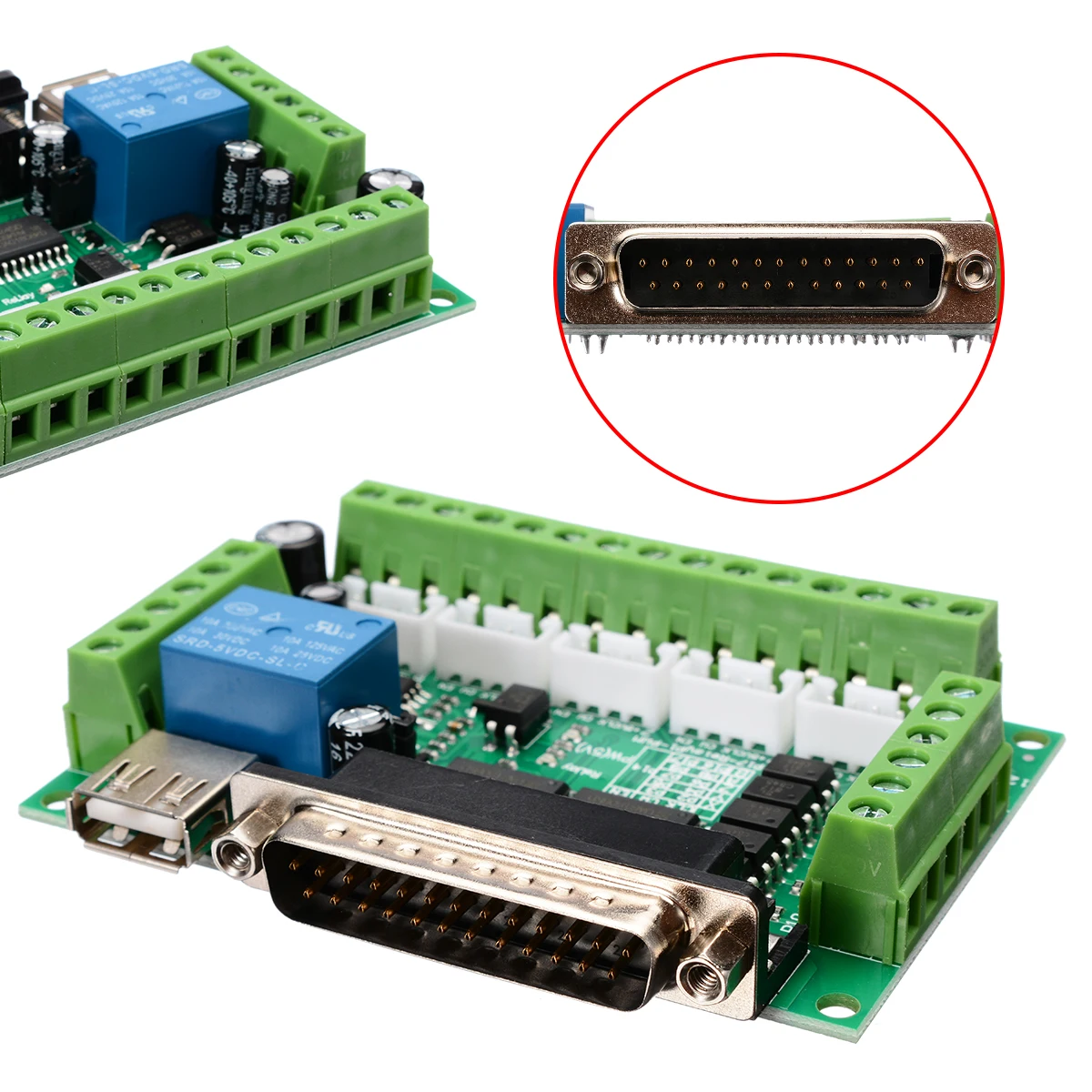
Just trying to get a feel for what I could expect.Ģ) Are there any benefit in using the Mesa 7I76e (ethernet) over the 6I25 - PCIE bus card, or just preference?
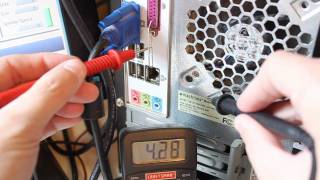
I have two general question with regards to linuxcnc with mesa cards.ġ) Should/Would one expect any noticeable difference in the performance or operation of linuxcnc when using something like the Mesa 7I76-6i25 combo, compared to a normal parallel port config. I'm currently using using linuxcnc 2.7 with a standard parallel port on a 2.8ghz intel core2quad processor, 16gb ram and a 4-axis cnc router, roughly 60" x 30" in size. MACH 3 is a very popular software package for CNC machines that enables motion control on a normal computer via a parallel port without the need for fancy.
